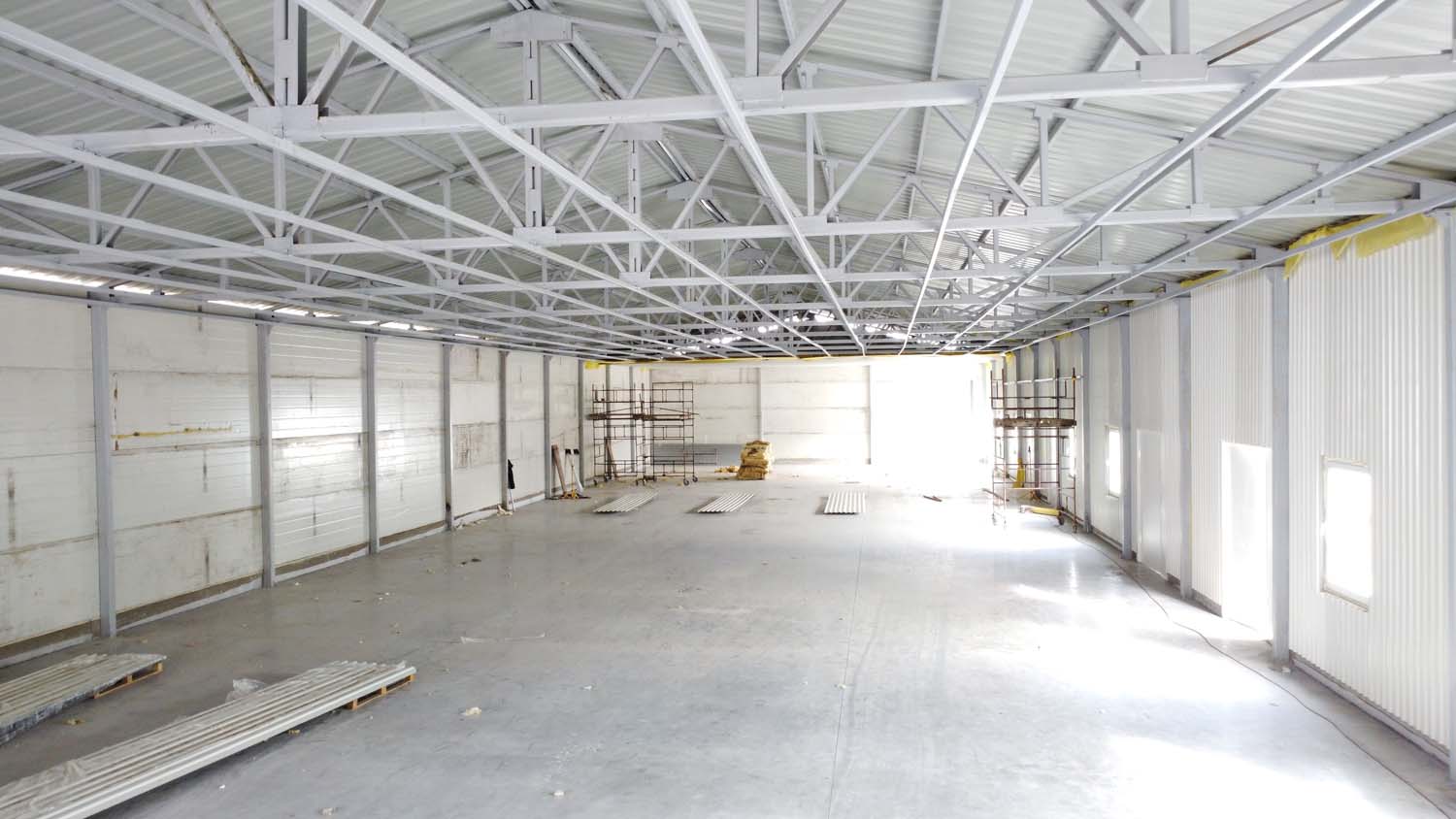
Magazynowanie towarów to jeden z fundamentów, na których opiera się nowoczesna logistyka firm należących do różnych branż. Jest to niezbędne dla utrzymania efektywności operacyjnej i skutecznego zarządzania zapasami, a także ograniczenia potencjalnych strat i zwiększenia satysfakcji Klientów. Jak wygląda przechowywanie i magazynowanie towarów w przedsiębiorstwie? Jakie procesy organizują pracę na magazynie? W dzisiejszym wpisie rozwiejemy wszelkie wątpliwości. Zapraszamy!
Spis treści
Czym jest magazynowanie towarów?
Magazynowanie towarów to skomplikowany proces, który opiera się na zarządzaniu ładunkami od chwili ich przyjęcia, aż po przygotowanie do dalszego przewozu lub wysyłki do odbiorcy. Celem tych czynności jest zagwarantowanie bezpieczeństwa i umożliwienie płynnej obsługi produktów na terenie całego magazynu. W rezultacie pozwala to na zachowanie ciągłości łańcucha logistycznego, przynosząc zyski danemu przedsiębiorstwu.
Na czym polega magazynowanie w przedsiębiorstwie? Proces ten można podzielić na kilka etapów:
- przyjęcie ładunku do magazynu – obejmuje to głównie jego rozładowywanie, weryfikację i kontrolę dokumentacji, a na końcu segregowanie i ewidencjonowanie nowo przyjętych produktów;
- przechowywanie towaru na stanie przez określony czas – w odpowiednich warunkach i zgodnie z wytycznymi;
- kompletacja zamówień – wybrane produkty są zbierane, kompletowane i przygotowywane do dalszego transportu;
- wydanie ładunku – transport do klienta lub wskazanego punktu odbioru.
Odpowiednie zarządzanie przestrzenią magazynową jest konieczne dla utrzymania efektywności pracy, zabezpieczenia towarów i ograniczenia kosztów operacyjnych na każdym etapie działalności.
Rodzaje magazynów
Można wyróżnić wiele rodzajów magazynów. Do najpopularniejszych kryteriów podziału należą typ konstrukcji obiektu, rozmieszczenie stref i miejsce magazynowania towarów, wysokość przechowywania, przeznaczenie magazynu i metoda składowania obowiązująca na jego terenie. Oto rodzaje magazynów z uwzględnieniem wytycznych.
Typ konstrukcji obiektu:
- magazyny zamknięte – nie są całkowicie zadaszone, ani zamknięte, co umożliwia składowanie ładunków na zewnątrz. Znajdują zastosowanie w magazynowaniu surowców budowlanych i kontenerów;
- magazyny półotwarte – posiadają częściowe zadaszenie, które zapewnia ochronę przed warunkami zewnętrznymi z zachowaniem łatwego dostępu do towarów. Idealne do przechowywania wielkogabarytowych produktów;
- magazyny zamknięte – obiekty są w pełni zamknięte i zadaszone. Służą do zabezpieczania produktów podatnych na wpływ czynników atmosferycznych, np. żywności i leków.
Rozmieszczenie stref magazynowych:
- rozkład przelotowy – przepływ towarów został w nich maksymalnie uproszczony: ładunki są przyjmowane w jednym wejściu i wydawane z drugiego, po przeciwnej stronie magazynu;
- rozkład kątowy – w tym układzie strefy sąsiadują ze sobą pod kątem, prostopadle; umożliwia to bardziej efektywne wykorzystanie dostępnej powierzchni;
- rozkład workowy – towary są w nim przyjmowane i wydawane po tej samej stronie; często wykorzystywany do składowania produktów w workach i pojedynczych opakowaniach, np. ziaren i chemikaliów.
Wysokość przechowywania:
- składowanie niskie – ładunki są przechowywane na niskich półkach, do maksymalnie 4 metrów nad ziemią. Zwykle używane w przypadku produktów o małej masie przeznaczonych do szybkiego wydania;
- składowanie średnie – wykorzystywane do przechowywania towarów na średnich wysokościach, do 7 metrów. Wymagają obsługi przez wózki widłowe;
- składowanie wysokie – systemy magazynowe powyżej 7 metrów; zwykle korzysta się w nich z regałów wysokiego składowania.
Funkcje magazynów:
- magazyny dostawcze,
- magazyny przeładunkowe,
- magazyny rozdzielcze,
- magazyny produkcyjne,
- magazyny kontenerowe,
- magazyny celne.
Wybrana metoda składowania:
- magazyny z elastycznymi miejscami składowania – ładunki są składowane w dowolnym, dostępnym miejscu;
- magazyny ze stałymi miejscami składowania – każdemu towarowi przypisano odpowiednie miejsce;
- magazyny z miejscami składowania uzależnionymi od rotacji ładunków – powszechnie stosowane w przypadku produktów spożywczych.
Zasady magazynowania towarów
W zależności od specyfiki danej branży i rodzaju ładunków, przedsiębiorstwa wykorzystują zróżnicowane zasady magazynowania towarów. Należą do nich metoda ABC, LIFO i FIFO. W powszechnym użyciu znajduje się również zasada 5S, której celem jest utrzymanie porządku i zapewnienie płynności procesów.
Metoda ABC
W metodzie ABC przechowywanie towarów odbywa się na podstawie ich rotacji. Produkty dzieli się na kilka kategorii: A – dla ładunków o największym obrocie wynoszącym ok. 80%, B – dla towarów o mniejszej rotacji, C – dla produktów najrzadziej wydawanych z magazynów. W zależności od kategorii, do której zostały przypisane, towary umieszcza się pod ręką lub w mniej dostępnych miejscach np. na dolnych i górnych regałach.
Metoda LIFO
Głównym założeniem metody LIFO (Last in First out) jest wniosek, że najnowsze ładunki są tymi, które jako pierwsze opuszczają magazyn. Dlatego produkty wprowadzone jako ostatnie znajdują się najbliżej strefy pakowania. Zasada LIFO jest stosowana w przypadku towarów pozbawionych ryzyka przeterminowania.
Metoda FIFO
Metoda FIFO (First in First Out) działa na zasadzie, że towary, które trafiły do magazynu w pierwszej kolejności, opuszczą go szybciej niż nowe ładunki. Dlatego, w przeciwieństwie do zasady LIFO, są umieszczane tuż przy strefie pakowania.
Zasada 5S
Zasada 5S to metoda organizacji pracy i przestrzeni wywodząca się z Japonii. Jest powszechnie stosowana w celu zwiększenia efektywności i poprawy bezpieczeństwa na magazynie. Dlatego opiera się na takich założeniach, jak:
- sortowanie – oddzielenie niepotrzebnych zasobów od tych używanych na co dzień;
- systematyka – uporządkowanie ładunków przy użyciu systemu oznakowań;
- sprzątanie – dbałość o utrzymanie czystości na magazynie;
- standaryzacja – ustalenie standardów i procedur dotyczących składowania towarów;
- samodyscyplina – ciągłe doskonalenie i wpajanie pracownikom nawyków w zakresie stosowania się do ustanowionych zasad.
Zaimplementowanie zasad przechowywania towarów w magazynach pozwala przedsiębiorcom na zoptymalizowanie przestrzeni, płynną obsługę produktów oraz zachowanie ich jakości przez określony czas przechowywania. W rezultacie prowadzi to do zwiększenia efektywności całego łańcucha dostaw.
Jak wygląda magazynowanie i przechowywanie towarów? Przebieg procesu
Magazynowanie i przechowywanie towarów w przedsiębiorstwie obejmuje kilka ważnych etapów, które wpływają na organizację i bezpieczeństwo składowanych produktów. Jakie są rodzaje procesów magazynowych? Całościowy obieg towaru obejmuje 4 fazy: od przyjęcia towarów, przez ich składowanie, aż po kompletację zamówień i wydanie ich do dalszego transportu. Oto krótki opis poszczególnych procesów magazynowych.
Przyjęcie ładunków
Proces magazynowania w przedsiębiorstwie rozpoczyna się od przyjęcia ładunków, czyli fizycznego odbioru towarów dostarczonych przez dostawców. Na tym etapie przeprowadza się kontrolę zgodności dostarczonych produktów z zamówieniem, zarówno pod kątem ilościowym, jak i jakościowym. Weryfikacji podlegają również dokumenty przewozowe, aby upewnić się, że wszystkie informacje się ze sobą zgadzają. Po potwierdzeniu przyjęcia towarów, są one odpowiednio oznaczane oraz rejestrowane w systemie magazynowym, co pozwala na ich śledzenie w dalszych etapach procesu.
Składowanie towarów
Polega ono na przeniesieniu przyjętych towarów na dedykowane im miejsca w magazynie. W zależności od rodzaju ładunku stosuje się odpowiednie metody składowania, np. na regałach wysokiego składowania, w pojemnikach czy na platformach. Proces ten wymaga dokładnego planowania, aby optymalnie wykorzystać przestrzeń magazynową i zapewnić łatwy dostęp do produktów. Wszystko musi odbywać się zgodnie z obowiązującymi normami, uwzględniając przy tym m.in. wymagane warunki temperaturowe czy wilgotność powietrza. Dlatego w powszechnym użyciu znajdują się systemy zarządzania magazynem (WMS), które często wspomagają ten etap, wskazując odpowiednie lokalizacje.
Kompletacja zamówień
Po etapie składowania rozpoczyna się kompletacja zamówień, czyli proces przygotowywania towarów do wysyłki lub wydania na produkcję. Zlecenia kompletacyjne są generowane na podstawie zapotrzebowania klientów lub wymagań produkcyjnych. Wybór odpowiednich produktów z miejsc składowania wymaga sprawności i dokładności, aby zminimalizować błędy i zapobiec potencjalnym uszkodzeniom. Proces ten może być realizowany ręcznie przez pracowników lub z wykorzystaniem systemów automatyzacji, takich jak roboty magazynowe. Nowoczesne technologie wspomagają szybkie i efektywne przemieszczanie towarów.
Wydanie ładunków
Ostatnim etapem magazynowania jest wydanie ładunków z magazynu. Wiąże się ono z fizycznym przemieszczeniem towarów do strefy wysyłek i przekazaniem ich klientowi lub na linię produkcyjną. Przed wydaniem następuje finalna kontrola, mająca na celu weryfikację zgodności przygotowanego zamówienia z dokumentacją. Wydanie towarów często wiąże się również z generowaniem odpowiednich dokumentów, takich jak listy przewozowe czy potwierdzenia odbioru. Są one niezbędne do dalszego śledzenia przepływu ładunków w łańcuchu dostaw.
Wyposażenie magazynu
Odpowiednie wyposażenie magazynu zapewnia bezpieczeństwo, efektywność oraz optymalne wykorzystanie przestrzeni. Aby dobrze zorganizować dostępną powierzchnię i zwiększyć wydajność operacyjną, nie może w niej zabraknąć takich elementów wyposażenia, jak:
- regały magazynowe – niezbędne do efektywnego przechowywania towarów o różnych gabarytach. Do wyboru są regały paletowe, wspornikowe, półkowe oraz systemy regałów automatycznych;
- systemy transportu wewnętrznego – obejmują wózki widłowe, przenośniki taśmowe, a także wózki ręczne i elektryczne, które usprawniają przemieszczanie ładunków wewnątrz magazyny;
- urządzenia do kompletacji i pakowania – stoły kompletacyjne, urządzenia do foliowania czy kartoniarki ułatwiają przygotowanie zamówień do wysyłki;
- środki bezpieczeństwa – lustra przemysłowe, bariery ochronne, siatki zabezpieczające oraz oznakowanie podłogowe, które minimalizują ryzyko wypadków;
- systemy informatyczne – oprogramowanie klasy WMS (Warehouse Management System) wspiera zarządzanie magazynem, umożliwiając precyzyjną lokalizację towarów i optymalizację operacji magazynowych.
Dobre wyposażenie magazynu nie tylko poprawia efektywność pracy, ale także wpływa na zwiększenie bezpieczeństwa personelu oraz ochronę przechowywanych produktów. Dzięki odpowiednim regałom, urządzeniom i systemom informatycznym możliwe staje się również utrzymanie długofalowej stabilności operacyjnej firmy.
Znaczenie efektywnego zarządzania magazynem dla sukcesu firmy
Magazynowanie towarów w przedsiębiorstwie to wieloetapowy proces, który obejmuje przyjęcie, składowanie, kompletację i wydanie ładunków. Każdy z tych etapów wymaga odpowiedniego zarządzania oraz dobrze zaprojektowanego wyposażenia magazynu, aby zapewnić płynność operacji oraz bezpieczeństwo składowanych produktów. Współczesne magazyny korzystają z zaawansowanych systemów informatycznych i urządzeń automatyzujących pracę, co pozwala na optymalizację przestrzeni, minimalizację kosztów oraz skrócenie czasu realizacji zamówień. Dlatego efektywne zarządzanie magazynem szybko przekłada się na sukces przedsiębiorstwa, gwarantując jego konkurencyjność i maksymalizując satysfakcję klientów.